Why the cheapest blast pot, is usually the most-costly choice!
In this article we’ll share our know-how on the most critical considerations when buying (or even renting) an industrial blast pot. This information is for professional sandblasters. Not hobbyists. The tips we’re providing are based on these upfront assumptions:
- This pot is a professional tool to increase your productivity and profitability
- You don’t want to pay more than you should.
If that describes you, we’re going to provide a checklist to help you select the perfect pot for your particular application. This article will save you lots of time, money, and headaches down the road. So, let’s jump right in.
Most people think that this is what you’re buying when you purchase a blast pot. It certainly appears to be a blast pot. But a blast pot is more than just a vessel holding your abrasive. It’s more than just a container.
If it were ONLY a vessel it would be very simple to buy the right pot. You’d compare size and price across the board – and simply choose the lowest price.
Here’s an analogy as to why that’s a bad strategy.
Let’s pretend you make your money as a taxi or uber driver. Would you buy this car from your local dealership?
From a container perspective, it holds 4 passengers and it’s most likely the cheapest car on the market.
Of course you wouldn’t waste your money. That’s not a car – it’s a frame. It can’t even provide the most minimal outcome you need… which is movement and transportation.
Likewise, as a professional blaster, the most minimal outcome you need from your pot is not storage, but conveyance. The movement and transportation of abrasive from the vessel, into the hose and out the nozzle.
The perfect industrial blast pot will provide 3 key benefits:
- Efficient Abrasive delivery
- Low maintenance and repair costs
- Pressure efficiency
These 3 benefits will determine your productivity, profitability, and ROI on the blast pot. And from here forward we’ll be discussing which blast pot features maximize each of these benefits.
But first – let’s just establish as TIP #1 this fundamental idea.
TIP #1
When pricing a blast pot, think of it as buying the valves and plumbing – more so than the vessel.
Just like a car, where the engine, transmission, and driveshaft determine speed, fuel efficiency, and future maintenance and repair… A blast pot’s results depend mostly on its valves and plumbing.
Size is important and we’ll discuss that in a moment, but your productivity and profitability are based on these metrics (3 Key Benefits) which are primarily the result of your valves and plumbing.
So with that being said, let’s focus on the number one valve to evaluate before making your purchase.
TIP#2
Focus on the abrasive metering valve.
The most important valve to consider is the abrasive metering valve. It can and will affect all three of these metrics (Efficient Abrasive delivery / Low maintenance and repair costs /Pressure efficiency) – and so therefore, pay attention to what is installed on the pot you buy – this may be the most critical choice for your success.
A really cheap blast pot costs less because it’ll have a really cheap metering valve. And a cheap metering valve will burn through your abrasive much faster.
Here are some fairly common conveyances of abrasive through blast pots per hour!
Garnet – 500 lbs / hour
Slag – 1100 lbs / hour
A cheap metering valve – on its own can be expected to waste roughly 5% of the abrasive that flows through it.
So in one year’s time, operating these pots at 6hrs/day – this is the abrasive you can expect to waste by saving money with a cheap metering valve:
Garnet – 500lbs x 5% waste x 6 hours x 5 days per week x 52 weeks = 39,000 lbs wasted per year
Slag – 1100lbs x 5% waste x 6 hours x 5 days per week x 52 weeks = 85,000 lbs wasted per year
Those figures are per year… and your blast pot should be at least a ten year investment!
Hopefully you can now see how the cheapest price upfront, can easily become the costliest decision on the back-end. And that’s only calculating wasted abrasive.
More Hidden Costs Of a Cheap Abrasive Metering Valve
- Burning through abrasive also results in your operators needing to stop and refill the pot more often. This refill process usually becomes an hourly 10-15 minute ritual of unproductive labor time – costing you money. In a ten hour day that’s almost 2 ½ hours of lost productivity.
- Using extra abrasive will also mean more clean-up time – which you guessed it, costs you money
- And finally, a cheap valve burning through abrasive will eventually require more replacement parts and maintenance – and this can realistically cost several thousand dollars per year. And if your metering valve were to break-down during your project for hours or even a day or more, what’s the value of that lost time?
Full Disclosure: We ONLY sell Axiom Schmidt blast pots. We’re not claiming they’re perfect, but from our nearly 50 years experience, they’re the best in the market. And maintenance and repair costs are just one of the reasons why.
Standard Metering Valve Maintenance Costs
- A standard inlet/outlet blast pot from competing brands will require around $2000 worth of spare parts per year. Replacing these valves every 1.5-2 months is the industry norm.
- Knock off pots that try and copy the Schmidt valves are longer lasting than the inlet/outlet competitors. However, due to the lower production quality, you are still spending about $1200/year on spare parts and replacement valves.
- The lowest maintenance blast pots are the Schmidt brand. They have a few different metering valves and systems, all which average between $350-$500 per year in maintenance costs.
Your abrasive metering valve is the precision instrument on your blast pot. It’s worth the extra few hundred dollars up front.
Tip #3
Choose the Best Pressure Efficient System.
There are two styles of blast pots:
- Pressure Release
- Pressure-Hold
A pressure release system acts in the following manner. When the deadman attached to your blast hose is activated, it sends a signal to pressurize the pot and convey abrasive into the hose and out the nozzle. Each time you release the deadman, it signals the pot to release this pressure into the air. The critical thing to understand here is that the pot needs to re-pressurize each time you depress the deadman. Even if pressurization only take a few seconds, you can imagine how much time is chipped away over the course of a day, week, or several weeks.
A pressure hold system, maintains pot pressure and doesn’t de-pressurize when you release the deadman. As soon as you depress the deadman trigger again, the blast hose is energized and the metering valve opens to release the flow of abrasive, in less than two seconds.
If you are doing blasting work that requires spot blasting, or constant stop/start moving about, you will save between 5-10% of your abrasive cost by using a pressure hold system. In fact, we recommend that all industrial blasters use pressure hold, its faster, and saves abrasive.
Okay, so what determines if the blast pot is pressure hold or pressure release? Surprise – it’s our old friend the abrasive metering valve. The valve you purchase even determines what style pot you’ll be using from here forward.
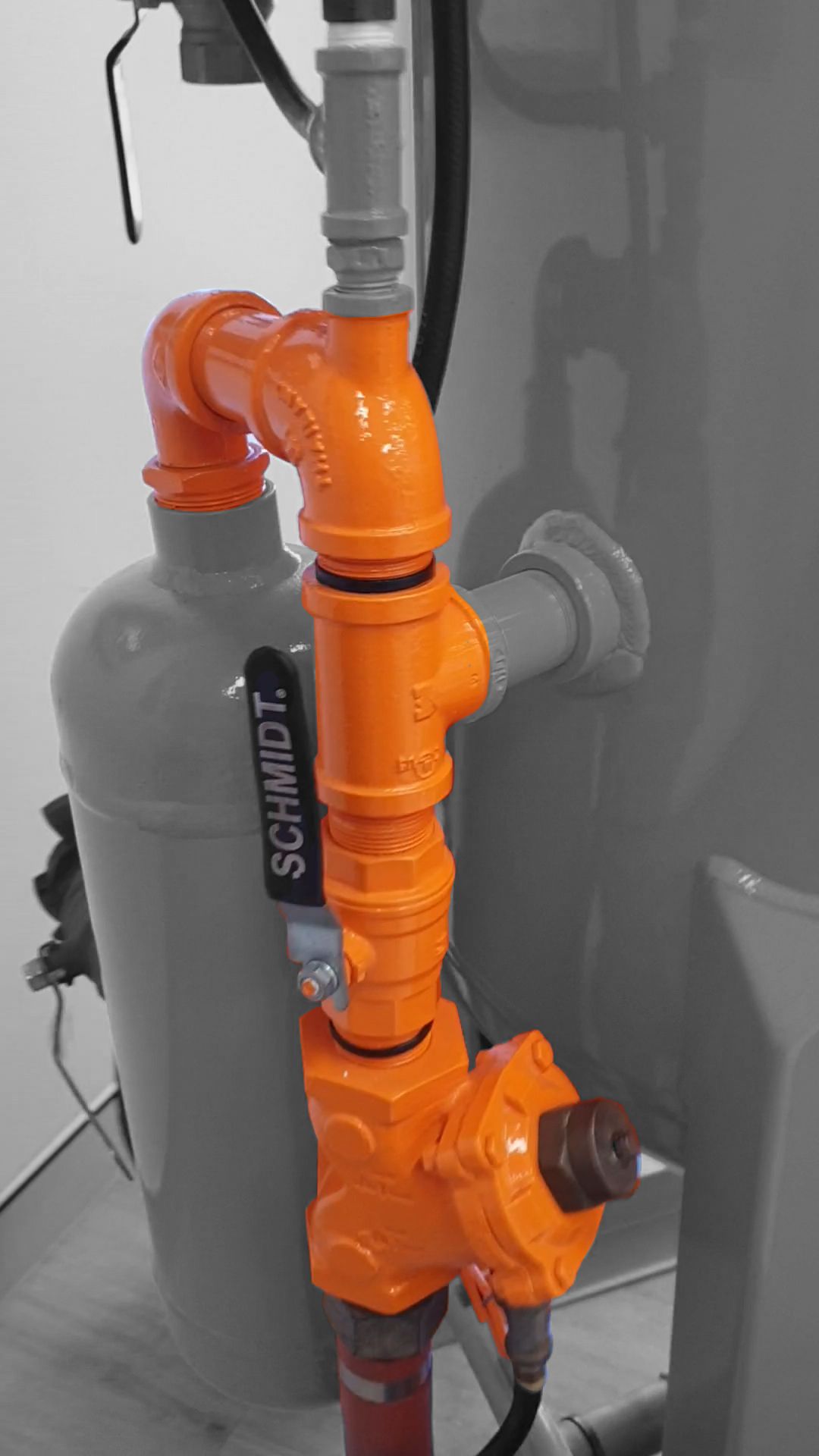
And in our experience, there are really only two reasons you should consider buying a pressure-release blast pot:
- You have an automatic overhead feed of abrasive into the pot. Which means when the pot depressurizes, gravity feeds abrasive into the vessel preventing those typical 10-15 minute labor breaks used refill the pot.
- A pressure-release metering valve costs less than pressure-hold, so this may depend on your budget.
Pressure efficiency also depends on maintaining optimal pressure. Any restrictions will negatively affect your blasting speed. On a blast pot, a component that can choke this pressure is the bore piping. These come in different diameters. Here’s our advice… For an industrial blast pot you want a minimum of 1.25” piping. Make sure this is the minimum. If you are going to be blasting with a #7 or #8 blast nozzle, you want to upgrade this to 1.5” piping. This allows you to maximize your pressure, getting more done, faster.
And finally, with such a variety of pot sizes we would never say size doesn’t matter.
Tip #4
Choose the Right SIZE For 80% of Your Application Needs
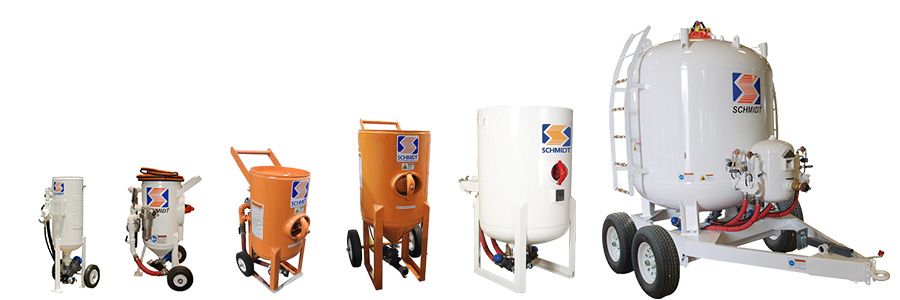
There are two main considerations for choosing pot size.
- Abrasive capacity
- Portability
The size of the blast pot impacts how long the blast pot will last before you have to stop and refill your abrasive. Ideally, this would be sized to ensure refills are few and far between.
For example, if you are blasting a large tank, you don’t want to have to stop to refill ever, so you would want a bulk blaster, but if your budget and transport options don’t allow for that, you want the largest pot that will suit your needs.
Of course, you may be involved with a variety of blasting scenarios, and in that case our recommendation is to choose the pot that will work for 80% of your work. If you don’t have the right pot for a future project, you can always rent.
The other impact of size is portability. If you’re needing a blast pot set up that allows you to go up a man lift, of haul around it around in the back of a pick up, then a smaller size is what you need.
In a blast room situation, you want to size the pot, so the blaster can refill during normal breaks. If the blaster needs to break every 1.5 hours for a convenience break, get a pot that will last that long.
So that’s the best professional advice we can offer in this article. We hope it helps clarify a few issues and saves you time, money, and headaches down the road.