Comprehensive Marine Solutions
BlastOne’s mission is to facilitate a Quantum Leap in surface preparation and finishing production across Shipbuilding operations. Our experience proves that when our recommendations are properly implemented – efficiency gains as high as 50% are consistently achieved.
BlastOne recognizes opportunities to assist the Navy significantly improve Blast & Paint lead times using:
- Adoption and Implementation of modern equipment and results-driven processes.
- Upgrading Existing Blasting and Painting Halls and Equipment to take advantage of the latest automation, ventilation, environmental control and abrasive handling technologies.
Blast and Paint Facility Design
BlastOne designs and builds the worlds most advanced and productive blast and paint halls for shipbuilding. 95% of all US shipyards fail to meet their blast and paint schedule, so BlastOne’s innovative technologies and system approach is designed to significantly reduce the bottleneck delays that plague America’s shipbuilding facilities.
Modern Blast and Paint facilities include automation and efficient processes which will boost shipyard production by up to 400%. Our proven blast and paint halls feature advanced ventilation, abrasive recycling systems, and humidity-controlled air to lower energy costs, enhance efficiency and prevent rework and waste.
MARINE BLAST AND PAINT HALL APPLICATION
BlastOne provides a diverse selection of high-performance products designed to meet the unique challenges of the marine industry:

Customized Blast & Paint Facility

Ship Module Paint Hall

Ship Blast & Paint Booth

Blast & Paint Hall With Roll-up Doors

Temporary Fast Track Blast & Paint Facility

Pass-through Production Blast Booth
A deep dive into our Approach and What to Expect
BlastOne delivers high-performance, cost-effective blasting and painting facilities through integrated design, construction, and long-term support. From concept to completion, we tailor solutions to client needs, reducing risks and streamlining processes. With 45+ years of expertise, we provide ongoing support, including maintenance, training, and readily available consumables, ensuring reliability throughout the facility’s life cycle.
ENHANCING OPERATIONAL EFFICIENCY THROUGH CAPACITY STUDIES
BlastOne’s Capacity Studies are designed to systematically analyze and improve the efficiency of blasting and painting operations. By assessing workflows and identifying bottlenecks, these studies provide practical solutions aimed at enhancing productivity and reducing costs.
Key Components of Capacity Studies:
-
-
-
Workflow Assessment
A thorough evaluation of current processes to identify inefficiencies.
-
-
-
Bottleneck Identification
Detection of areas that impede productivity.
-
-
-
Implementation of Solutions
Application of targeted improvements tailored to specific operational needs.
-
-
Sustained Efficiency
Development of strategies to ensure long-term operational gains.
-
Shipyard Painting and Facility Design Considerations
Presented for the Society of Naval Architects and Marine Engineers (SNAME)

CASE STUDY: LARGE USA SHIPBUILDER, A CAPACITY STUDY LED TO SIGNIFICANT IMPROVEMENTS:
-
40% Reduction in Production Time: Project timelines decreased from 4 weeks to 2.5 weeks.
-
45% Increase in Throughput: Enhanced output without additional resources.
-
65% Reduction in Material Waste: Optimized material handling processes.
-
80% Decrease in Operational Delays: Minimized downtime and rework, improving workflow efficiency.
HAVE A QUESTIONS ABOUT OUR CAPACITY STUDIES?
Connect with our marine project experts today for a Free Consultation
on your facility or shipbuilding needs.

Naval Vessel Maintenance
60% OF US NAVAL VESSEL MAINTENANCE IS MISSED OR DELAYED
-
-
-
Inefficient Blast and Paint Operations
Blast and paint make up 53% of maintenance schedules but only account for 20% of the total cost. Delays in this critical-path process cascade across the entire project, causing significant disruptions.
-
-
-
Aging Infrastructure and Equipment
Many naval shipyards still reply on 40+ year old equipment and facilities, leading to inefficiencies, longer reproduction cycles, and frequent breakdowns.
-
-
-
Limited Capacity and Resource Constraints
With a limited number of shipyards handling a growing workload, maintenance backlogs occur, slowing progress and compounding delays.
-
-
Ship Maintenance
SHIPYARD BLASTING INNOVATIONS
BlastOne has developed a range of solutions and equipment to lower the cost and timeline that shipyards spend doing abrasive blasting. Many of these innovations have lead to production improvements of up to 65%.
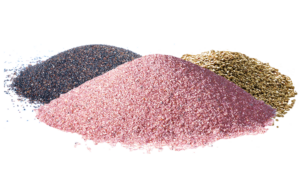
MarineBlast Garnet – an Engineered Blend of Abrasive Media
Precision-engineered abrasives for efficient rust and scale removal, ideal for preparing vessel surfaces for coating.

Snakebite – Silenced Blast Nozzles
Snakebite, the Worlds quietest blast nozzle reduces the noise of abrasive blasting by 16dB. This is designed to reduce the 100’s of hearing loss claims every shipyard gets per year.

Vertidrive Robotic Automation
Advanced magnetic blasting robots like the VertiDrive M7 can blast the externals of naval vessels 5x faster then the industry norm, reducing the time the vessel is out of service.
NEED HELP SELECTING THE RIGHT EQUIPMENT FOR YOUR MARINE PROJECT?
Check out our Blasting and Spray Equipment Buying Guides for detailed recommendations tailored to your needs.
OPTIMIZING SURFACE PREPARATION: THE PEATS ADVANTAGE
-
-
Process (P)
We decide what is the process and/or method of surface preparation for the project at hand, taking into account any unique challenges.
-
-
-
Equipment (E)
Determine which equipment combination will give you the safest and greatest performance.
-
-
-
Abrasive (A)
Different jobs may require different abrasives. Working from the specification and application backwards, we select the right abrasive to most efficiently achieve the results required.
-
-
-
Technology (T)
IntelliBlast providing real-time results from the field to ensure operations requirements and expectations are being met, and exceptions are being managed.
-
-
Sustain (S)
Follow through on the improvements made through real-time monitoring, onsite support, on-the-tools training and regular reporting.
Case Studies

MODERN ENVIRONMENTAL CONTROLS ENSURE A SAFER, MORE EFFICIENT SHIPYARD.
“This improved facility allows for larger portions of ships to be prepared and painted with modern environmental controls, ensuring our shipyard remains one of the safest, most efficient, and environmentally responsible in America.”
— Pierroberto Folgiero, CEO of Fincantieri

DOUBLING PRODUCTIVITY WHILE ACHIEVING ZERO PARTICULATE EMISSIONS.
“BlastOne’s engineering and equipment have enabled us to cut our particulate emissions to zero while doubling our productivity. VT Halter Marine is delighted by the finished facility.”
— Tim Pryor, Facilities Manager of VT Halter Marine

LEADING NORTH AMERICA IN MODERN SHIPBUILDING FACILITIES.
Irving Shipbuilding now has the most modern shipbuilding facilities in North America in Halifax, Nova Scotia.
— Irving Shipbuilding
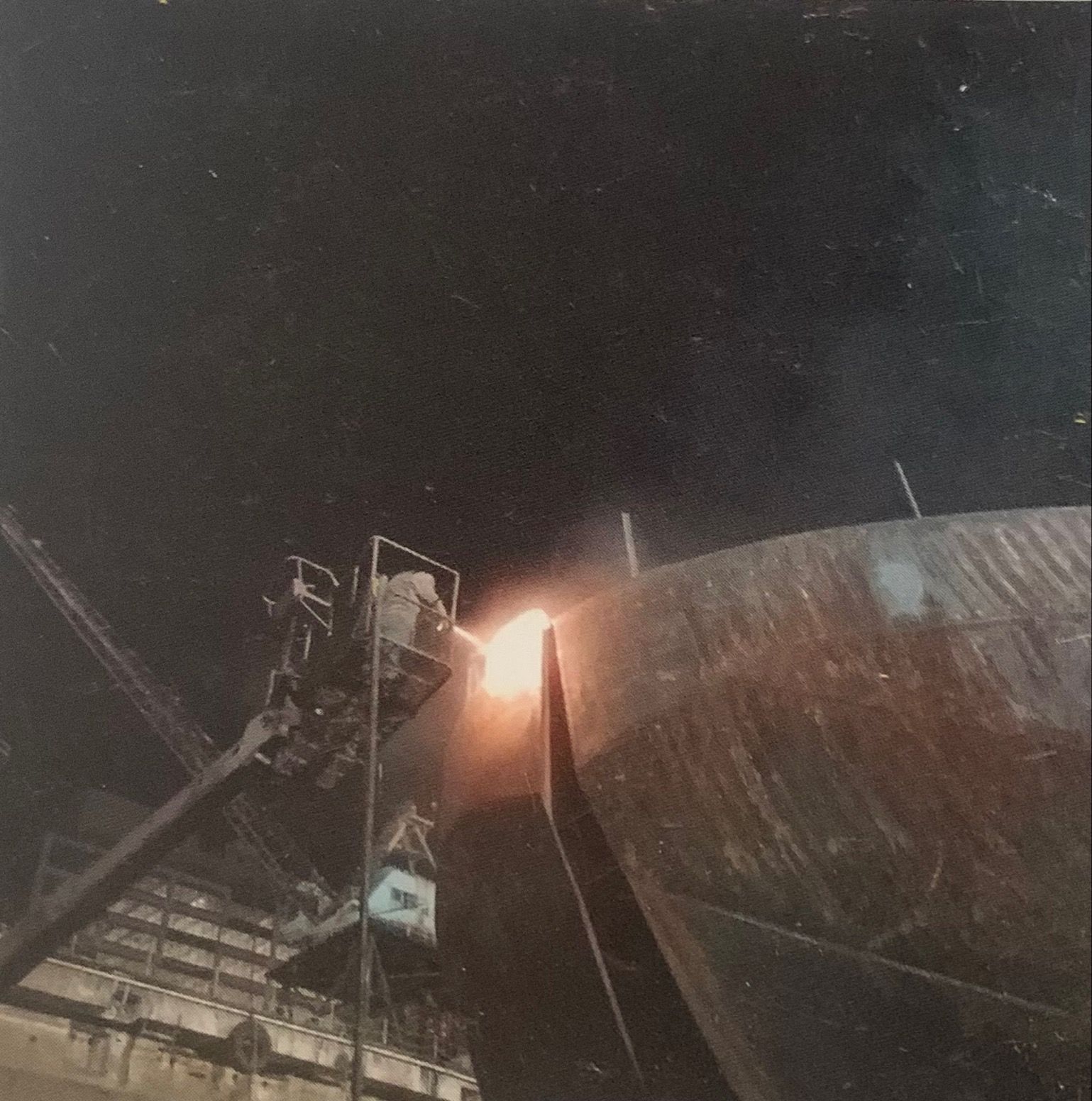
AHEAD OF SCHEDULE AND EXCEEDING EXPECTATIONS WITH BLASTONE GARNET.
The East Coast Shipyard utilized BlastOne Garnet and modern equipment in their blasting operations, significantly increasing productivity and enabling the completion of a twin barge project ahead of schedule.
— East Coast Shipyard

REVOLUTIONIZING MAINTENANCE TURNAROUNDS WITH VERTIDRIVE M7.
One Vertidrive does the work of 5-7 men. Implementing the VertiDrive M7 allowed the team to achieve faster maintenance turnarounds while maintaining high-quality standards.
— Large Shipyard
Real Solutions, Real Impact: See the Results
Industry & Project Challenges
Marine blasting and painting projects face numerous challenges, which require innovative solutions and careful coordination. These challenges stem from the complexity of maintaining large marine vessels and the unique demands of shipyard environments. Below is a comprehensive breakdown:
-
-
Tight Deadlines
Minimized Downtime: Ships are docked for limited periods, and every hour out of service results in financial losses. Rust removal, blasting, recoating, and floating must be completed efficiently to meet schedules.
Concurrent Repairs: Overlapping blasting and coating with other fabrication work can lead to delays, as these tasks cannot always be performed simultaneously.
Equipment and Weather Delays: Downtime caused by equipment breakdowns or adverse weather conditions adds to scheduling pressures.
-
-
-
Unpredictable Scope of Work
Unknown Damage: The condition of coatings and surfaces is often unclear until vessels are docked or ballast tanks are inspected, requiring flexibility in planning and resources.
Corrosion Risks: Severely corroded areas may necessitate unexpected welding and fabrication, further increasing timelines and costs.
-
-
-
Confined Spaces and Accessibility
Challenging Work Areas: Ballast tanks, ship holds, and other confined spaces require specialized equipment, lighting, and ventilation to ensure safe and efficient operations.
Logistical Constraints: Equipment often needs to be craned on and off ships, demanding precise coordination. In slipways, the angled positioning of vessels adds further complexity.
-
-
-
Environmental Challenges
Dust Control: Abrasive blasting produces significant dust, which must be contained to prevent impacting other trades and nearby residential areas. Additional containment measures increase project costs.
Noise Management: Noise generated by blasting operations must be minimized to avoid disturbing on-board crew, shipyard workers, and surrounding communities.
Waterway Contamination: Strict regulations require heightened levels of containment to prevent abrasive or coating waste from polluting waterways. Heavy fines may be incurred for non-compliance.
Waste Disposal: Managing and disposing of waste materials in compliance with environmental standards adds logistical and financial complexity.
-
-
-
Safety Challenges
Hazardous Confined Spaces: Working in confined spaces poses risks such as toxic gas buildup, poor ventilation, restricted access, and communication difficulties.
Operator Fatigue: High-thrust blasting activity and long shifts can lead to operator fatigue, increasing the risk of errors and injuries.
Workplace Incidents: Crowded conditions with multiple trades working simultaneously elevate the likelihood of workplace accidents.
Fall and Equipment Hazards: Working at heights and handling heavy equipment introduces significant safety risks, requiring robust safety protocols and training.
-
-
-
Crowded Workspaces
Multiple Trades at Once: Welders, painters, blasters, inspectors, and crew members working simultaneously create congestion, slowing productivity and complicating operations.
Stand-Down Crew: The presence of additional personnel on board further challenges safe and efficient project execution.
-
-
-
Quality Assurance Challenges
Stringent Standards: Meeting high-quality requirements necessitates frequent inspections, which can delay progress.
Inconsistent Results: Issues such as uneven blasting pressures, poor visibility, and abrasive embedment compromise coating adhesion and surface cleanliness, leading to rework and higher costs.
-
-
Cost Overruns
Labor Inefficiencies: Excessive man-hours required for blasting increase labor costs.
Material Wastage: Inefficient abrasive usage and containment measures drive up material expenses.
Budget Variations: Unforeseen damage, delays, and scope changes often result in budget overruns, impacting profitability.
Marine Resources
Corrosion Control Solutions for the Marine Industry
Shipyard turnarounds can be complex and time-consuming. This report outlines key strategies to improve efficiency and reduce downtime in blasting and painting operations. It covers best practices, process optimizations, and solutions to help shipyards complete projects faster.
25 Important Considerations when Building a Blast Facility
If you are purchasing a turnkey blast room for building it yourself, there are 25 subjects you need to be well versed in. BlastOne has compiled a detailed report containing an in-depth guide on all the critical components of a blast room: design considerations, abrasive education, and production techniques.
Knowledge & Learning
Videos from the Experts
How to | Primed Insights | Safety Tips
VT Halter Case Study
Chloride Field Testing Demonstration
Fairhaven Shipyard Testimonial
Industries Served
Contact BlastOne
We love to talk to customers and help them make the best decisions when purchasing equipment.
You can reach us via our Live Chat, Email, Phone, and Online Form.